Are you a contractor?
Join our network and attract real clients!
Why and How to Lockout Hazardous Materials
By Editorial Team
Updated on February 9, 2024

Workplace safety is an overwhelming challenge facing all industries, most notably those dealing with hazardous materials. The construction industry as a whole is highly concerned about this problem, especially since it revolves around significant hazardous energy-related risks. Hence why lockout devices on hazardous materials are essential for ensuring the safety of worksite labourers. In this article, we’ll delve into the reasons why it's paramount to establish such a practice.
What is a hazardous energy lockout?

A lockout, or lockout device, allows for neutralizing energy sources and prevents tragic on-site work accidents.
Hazardous Energy-Related Risks
The first reason for enforcing a lockout device on hazardous materials is because of their inherent risks. Hazardous materials most notably include, but aren’t limited to, the following:
Electricity
Compressed gas
Hydraulic and pneumatic energies
Chemical substances
And others
These above-listed energies can lead to severe, possibly even deathly, accidents if not properly regulated and controlled.
Electrocution Risks
One of the most common risks is electrocution. In fact, many energy sources, such as electrical systems, can cause potentially lethal electric shocks if ineffectively controlled. For example, when electrical equipment is undergoing maintenance or repairs, it’s essential to establish a safety device (lockout) to prevent any sort of accidental triggering that may put the workers' lives in danger.
Fire Hazards
Moreover, hazardous energies can also be triggered by explosions or fires. When flammable substances are exposed to an energy source, such as a flame or electric spark, fire-hazardous materials can quickly go up into flames, causing severe material and bodily injuries—it could potentially result in the death of persons present.
Health Risks
Hazardous materials can also present health risks. Toxic chemical products can, for example, lead to nefarious health side effects should on-site workers inhale, ingest, or come in direct contact with such substances. Therefore, it becomes primordial to have lockout devices around such substances, limiting their access to prevent non-controlled exposures.
Accident Prevention: When to Use Lockout Devices

Hazardous materials must be kept behind safety devices in the event that their access might risk the safety of individuals or the environment itself. This may include situations in which they’re stored in areas accessible to the public, in warehouses, industrial sites, or during transportation.
One of the benefits of a lockout is that it allows workers to safely carry out maintenance operations. By restricting access to these energy sources with a safety device, workers are protected against electric discharges, gas leaks, or fluid explosions. These prevention measures allow for repairs or other interventions to be carried out with peace of mind, negating the risk of potentially life-threatening injuries.
It’s primordial to raise awareness and train workers regarding the risks associated with these energies to ensure hazardous materials are effectively locked out.
Companies must establish regular training programs to educate their staff about the appropriate procedures and provide them with the necessary knowledge to identify hazardous energy sources and safely neutralize them.
Who is responsible for lockout procedures?
Adding safety devices to hazardous materials isn’t the sole responsibility of companies. It’s a shared responsibility between several parties:
The owner of the company is the first person responsible for implementing a lockout program to ensure the safety of their personnel. They must ensure that all dangerous machines are identified and labelled with the appropriate lockout/tag out.
Supervisors also have a key role in the process. They must train and inform employees about procedures, ensure lockout devices are used correctly, and supervise work operations where lockout devices are used.
Employees are also responsible for adhering to established procedures and correctly employing safety devices. They must also flag all machinery that isn’t properly locked out to their supervisors.
Regulation: How to Establish a Lockout Procedure

In Canada, a lockout procedure for hazardous materials is regulated by the Occupational Health and Safety Act, along with federal and provincial safety standards. Concerned parties need to be knowledgeable about, and adhere to, these standards to establish an effective and safe management of hazardous energies.
Standards Regulating the Use of Lockout Devices (STANDARD CSA Z460)
Here are the main guidelines for a lockout procedure:
1. Identify hazardous materials
It’s important to identify all hazardous materials found in a workplace. This may include, but isn’t limited to, the following:
Toxic products
Flammable products
Corrosive products
Compressed gas
And others
2. Risk assessment
A risk assessment must be carried out to determine potential threats associated with these hazardous materials. This will help establish the appropriate lockout procedures for every piece of equipment or machinery employing these hazardous substances.
3. Establish lockout procedures
Based on risk assessments, the procedures must be developed for specific equipment utilizing hazardous materials. This implies implementing locking mechanisms (locks, labels, etc.)—to prevent staff from accidentally turning on machinery—and safety devices to protect employees while carrying out maintenance operations, servicing, or repairing equipment.
4. Training and awareness programs
All employees must be properly trained and made aware of lockout procedures regarding hazardous materials. This includes risk awareness, lockout device identification, lockout procedures, the use of personal protective gear, etc.
5. Implementing lockout procedures
Lockout procedures must be systematically applied every time a machinery utilizing hazardous materials requires maintenance, servicing, or repairs. Locking mechanisms must be installed before carrying out any intervention on equipment and must remain in place throughout the entire servicing process.
6. Verification and follow-up
Lockout procedures must be regularly verified to ensure they’re correctly applied and followed. Supervisors must conduct periodical inspections to ensure the lockout devices are correctly installed and that all employees are adhering to the established lockout procedures.
How to Structure Lockout Procedure Elements
A hazardous material lockout document provides detailed information regarding the lockout and tag out procedures used to safely isolate and prevent access to equipment, machinery, or installations containing hazardous materials or substances. The lockout procedure document must include the following elements:
Operation identification: A list of specific tasks during which a lockout procedure should be implemented.
Equipment description: Clear instructions regarding the type of equipment or machine requiring a locking mechanism, including location and identification details.
List of related hazards: A directory of the potential risks associated with hazardous materials or equipment.
Lockout procedure: Detailed description of the steps to follow to safely isolate the equipment in question.
Responsibilities and authorizations: A list of the individuals responsible for implementing the procedure as well as necessary authorizations.
Removal and verification instructions: Detailed steps to follow to remove a lockout device once the work is completed; the measures to take to ensure the equipment is safe to operate.
Emergency plan: Guidelines to adhere to in the event of an incident or accident involving an employee, equipment, or hazardous materials.
In a nutshell, a lockout procedure document regarding hazardous materials is an essential tool to ensure the safety of workers by establishing strict lockout and tag out protocols to prevent accidents related to hazardous materials.
What does the CNESST say about a lockout?
The CNESST (Quebec's Occupational Health and Safety Program) defines a lockout as a procedure enabling the neutralization of hazardous energy sources (electrical, mechanical, thermal, hydraulic, etc.) of a machine or equipment during repair, maintenance, or servicing procedures.
The CNESST recommends lockout devices to prevent workplace accidents related to sudden releases of potentially hazardous energy, such as unintentional machine ignition, shifting pieces, fluid overflow, gas emissions, etc.
It encourages employers to:
elaborate a lockout policy;
train workers on lockout procedures to follow;
use the appropriate locking and tag out devices; and
regularly inspect equipment and procedures to validate effectiveness.
Other Hazardous Energy Management Programs or Methods

Besides lockout devices, there are other methods used to control hazardous energies that may be used on top of or instead of lockout mechanisms. Here’s a list of the main ones.
Machine Tag Out
This method consists of labelling machines to warn workers of the associated risks of using said machines and the presence of hazardous energies.
Zero Release
This is a method that consists of ensuring all machine-related energy sources are neutralized or isolated before carrying out maintenance or repair work.
Lockout/Tag Out Protocols
This method infers the use of specific procedures to lockout or tag out machines to prevent accidental startups during work operations.
Work Permit System
This system mandates workers obtain a permit before carrying out operations requiring the use of potentially hazardous equipment or machines.
Mechanical Protections
This method consists of installing safety devices on machines to prevent workers from accessing hazardous zones during work operations.
Training and Awareness Programs
Educating workers regarding the risks associated with hazardous energies and the appropriate control methods used to ensure their safety in the workplace.
Emergency Procedures
On top of preventive control measures, it’s important to establish emergency procedures to effectively deal with emergency situations related to hazardous energies, such as chemical product leaks or fires.
To ensure hazardous energies are effectively managed, the key is developing the right method or most suitable program based on a specific work environment.
A Fundamental Part of Workplace Safety
Lockout devices on hazardous materials are must-haves, ensuring the safety of workers in the workplace. By neutralizing hazardous energy sources, you can prevent serious accidents and save lives. However, bear in mind that a lockout isn’t the sole tool used, additional steps must be carried out to effectively manage hazardous energies. Raising worker awareness and providing them with adequate training are also important steps to guarantee the effectiveness of this practice. By adopting these measures, construction industry companies can create safe work environments in which hazardous material-related accidents are kept to a minimum.
Get new contracts for your construction or renovation company
RenoQuotes.com can help you get new contracts. We get new project proposals from clients seeking top-rated and trustworthy renovation professionals like yourself. To get started, simply fill in the form on our homepage (it only takes a few minutes) and receive information regarding potential clients by way of our services.
Dial 1-844 828-1588 to speak with one of our customer service representatives.
Looking for something else?
Related articles
The latest industry news, interviews, technologies, and resources.
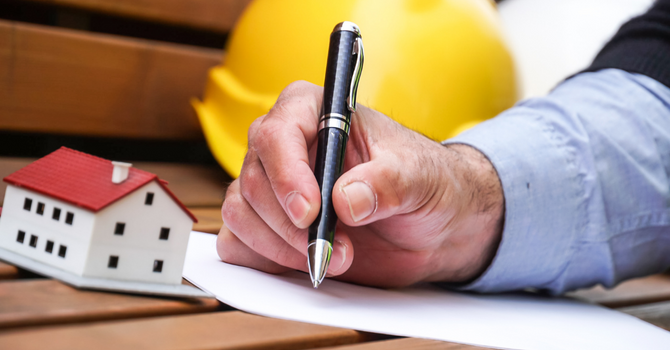
Amanda Harvey
•07 Nov 2023
For an entrepreneur, receiving a large number of requests for various projects bodes well for business. However, your phone ringing off the hook shouldn't be enough to reassure you.
Editorial Team
•30 Jan 2025
As a renovation contractor, are you already thinking about the overwhelming amount of jobs you’ll have during peak business periods? Albeit a busy, hectic schedule is nothing but good news, organizing your schedule accordingly may be a job on its own!
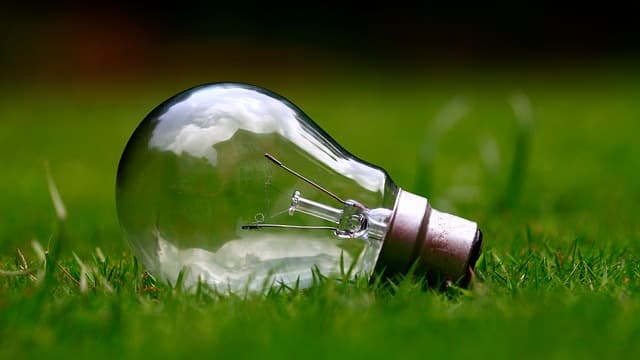
Editorial Team
•07 Nov 2023
Our homes are complex systems that are multifunctional and multi-faceted with a lot of various parts. Thus, it is important for our homes to run smoothly and efficiently like well-oiled machines. All machines need energy to operate, and as most homeowners know, our homes consume a large amount of energy annually.

Editorial Team
•07 Nov 2023
Painting the façade of a house can be a long and arduous process. However, if the work is carried out well, the transformation can be rather drastic! When a quality product is applied to a well-prepared surface, said painted surface will have a longer service life.
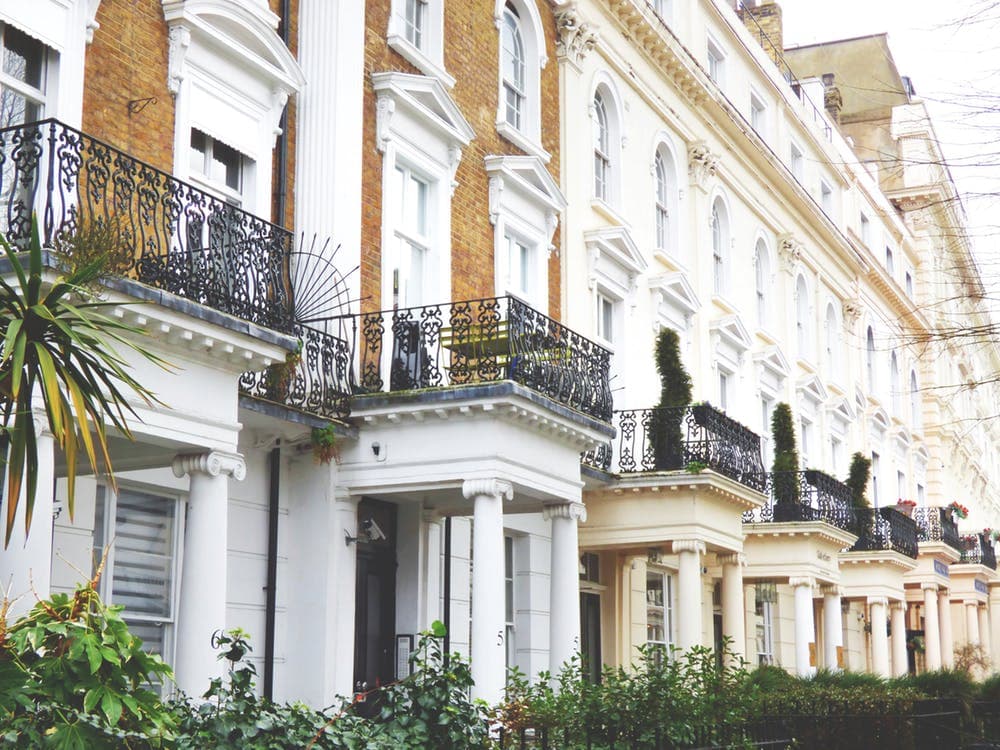
Editorial Team
•07 Nov 2023
Outdoor columns on the facade of your home add an element of originality and allure. Whether used for your landscaping, porch or walkways, incorporating columns into your design can have a lasting appeal. However, since these columns are outdoors, they are exposed to various forms of weather damage. Therefore, it’s important to know how to care for your outdoor columns.